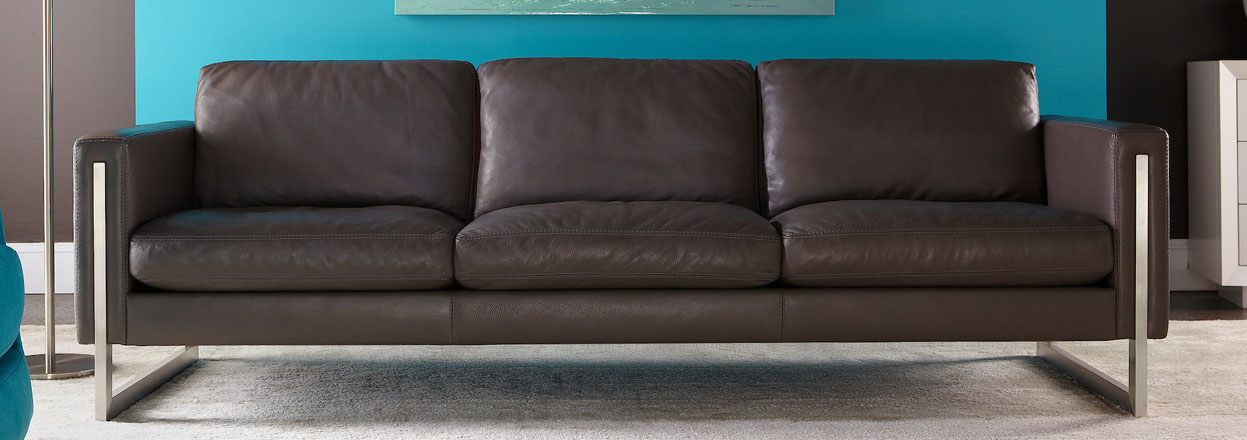
History
Leathermaking is one of the oldest industries in the world. Leather has been produced and used by humans in various ways for thousands of years. Early civilizations around the world figured out how to use animal skin for clothing, tools and shelter as evidenced by the discovery of leather artifacts dating back to 1300 BC. Vegetable tanning was originally invented by ancient Hebrew settlers, while the ancient Greeks used started using their own techniques around 1200 BC. Leathermaking eventually spread to Egypt, and then to Rome.
Leather Tanning
Leather is a fibrous material constructed as a three-dimensional network of interlacing fibers in a way that cannot be duplicated by man-made products. Its composition gives it exceptionally useful and desirable qualities such as flexibility, adaptability to change, the ability to breathe, and thermal insulation. One of the beauties of leather is that each hide is unique, an original work of nature. Each hide has its own nicks, scratches, wrinkles, veins, and grain and shade variation. Leather is preserved by the tanning process, during which animal hides are transformed into soft, pliable leather through a series of chemical treatments. Its primary purpose is to convert the raw collagen fibers of the hide into a stable product that is no longer susceptible to decomposition. Throughout most of the history of leathermaking, vegetable tannins were used. It wasn’t until the 19th century that other more efficient and less costly alternatives were discovered. The process begins by curing, or preserving, the hides in salt in a packing house to protect the raw material from bacteria until the pre-tanning process begins at the tannery.
Many of the steps in tanning and finishing the hides are accomplished by immersing them in a liquid chemical bath that is contained within a rotating drum, allowing the various solutions to completely penetrate the thickness of each hide. In the first of these processes, the hides are washed and soaked to remove excess salt and foreign substances and to restore the fibers to their natural condition so that they will readily absorb tanning agents. The next step in the pre-tanning process, liming, occurs when a strong alkaline lime solution is used to loosen and remove the hair, which has a swelling effect on the leather. The tannery then mechanically splits the hides horizontally in this swelled state, yielding two and sometimes three layers, or splits. It is the top layer, or grain, that is used for upholstery leather and is the most valuable part of the hide. The center split is often referred to as suede. The bottom layer is used for items such as shoe and belt linings as well as low-priced personal leather goods. The hides are then delimed in the drum to remove the alkalis. A weak enzymatic treatment called bating is used to make the grain finer and smoother, and to restore elasticity to the leather. Finally, during the pickling stage of pre-tanning, the hides are soaked in an acid solution to ready them for accepting the tanning materials.
Tanning itself is achieved by saturating the hides with tannins, molecules that easily bond with proteins and draw out liquid. The two most commonly-used tanning solutions are vegetable tannins and mineral tannins. Chromium sulphate solution (“chrome”) is the most popular mineral tannin – it is typically used for upholstery leather.
Vegetable tanning is extracted from the leaves, bark and wood of such trees as oak, chestnut and hemlock. The hides are suspended from racks in vats containing the tanning solutions, where they are left to soak. They are then bleached and “stuffed” with natural oils and greases. The resulting leather is firm and thick. Most shoe soles, luggage, handbags and belts are made from vegetable tanned leather. Chromium tanning was developed in the nineteenth century to serve three purposes: to speed up the tanning process, to make the hides more flexible and supple, and to prepare them to accept color uniformly. This type of tannage is carried out by using chromium sulphate, a mineral salt which penetrates the hide rapidly, completing the process in a day or two. The hides are tumbled in huge rotating drums partly filled with a chrome salt solution for up to 24 hours. The leather is then cleaned, dried and smoothed in preparation for bleaching and dyeing. Chromium tanned leather is resistant to the effects of harmful air pollutants. In addition to being efficient and cost-effective, chromium tanning results in a thinner leather that has high stability, strength, softness, and mechanical flexibility, as well as excellent dyeability and color fastness. It can be dyed into an unlimited array of colors, which makes it particularly desirable for upholstery and fashion.
Post-Tanning Treatments
The goal of post-tanning is to upgrade the leather and make it more suitable for its intended use, whether it’s upholstery, garments or accessories. It improves the hides’ external appearance and enhances their flexibility, firmness, rigidity and strength. The hides are then mechanically shaved to make them a uniform thickness throughout.
Finishing
Finishing determines the final look and feel the leather. The purpose of finishing is to protect and enhance the surface appeal of the leather. It also minimizes the appearance of blemishes, without sacrificing the natural look and feel of the leather. During this final stage, the hides receive their ultimate color, protection (against abrasion, heat, light, liquid and dirt), texture, sheen, and any special effects, such as antiquing. The way in which a particular dyelot of leather is finished depends on its intended use.
Dyeing means applying the desired color to tanned leather by applying coloring agents, or dyes. The dyes also improve the appearance of the leather, making it more suitable for its intended purpose. During the first phase of the finishing process, the hides are placed in rotating drums, into which dyes are added through central tubes. The type of dye used is aniline, which is water-based and has the ability to enter the leather and bond with its fiber structure. It can take up to 24 hours for the hides to completely absorb the aniline dye. They are then fatliquored, another chemical process using either natural or synthetic oils or fats, which lubricates their fibers and makes them softer and more flexible, with an appealing surface hand. After drying, any hides with unsightly surface defects, such as insect bites and healed scars, are mechanically buffed with abrasive paper to “correct” the grain and clean the flesh side of irregular fibers. Full-grain leather, or leather that does not require cosmetic buffing, is polished with a velvet wheel. Finally, the hides are passed on a conveyor belt through a spray line where they receive a topcoat spray with a different degree of coating, depending on the intended look and use of the leather. This final topcoat perfects the color and adds topical protections.
Plating
The final processing step involves plating the hides under high pressure and heat to smooth the surface of the coating materials that have just been applied. Usually, the surface of the plate is mirror-smooth, but sometimes a specially engraved plate is used to produce a particular pattern or embossment, such as imitation ostrich and reptile. However, as is often the case with corrected leather, the plate is designed to mimic the natural grain of leather and replaces the natural texture which has been removed during the buffing process.
The hides are then trimmed and measured, and are ready for shipment to their purchaser.